The Duravit CEO answers questions about the laying of the foundation stone for the new production plant in Matane, Canada.
1. Mr Tahy, Duravit AG is investing a high double-digit million-dollar amount in the construction of a new ceramic plant in Canada. Could you please explain the background of this project?
First and foremost: For Duravit, this is the largest investment in our company’s history. It fills me with pride that we have now been able to give the go-ahead for this extraordinary project. At the same time, I feel gratitude for the trust that our owner family has placed in us.
The new plant is a milestone for Duravit in several aspects: We are setting standards for the responsible use of resources by replacing natural gas as a fossil fuel with sustainably generated energy from hydropower. In addition, we have made our supply and logistics processes sustainable to strengthen our presence in the growth market of North America with our own local production facility. Not to be forgotten: Around 240 new jobs will be created at the new site.
None of this would have been possible without the support of our local partners: the responsible Québec, and the city of Matane. With Hydro-Québec as our energy supplier, we also have a long-term partner for the supply of affordable and, above all, clean energy.
2. The new plant in Matane, Canada, is a central element in Duravit’s sustainability strategy. What does that mean specifically?
We have set ourselves the ambitious goal of climate-neutral production by 2045. The production of ceramics is one of the most energy-intensive industries. A lot has changed here in recent years, and energy and resources are now used much more efficiently. Nevertheless, we need a disruptive change in ceramics production that tackles the CO2 emission problem at the root when using natural gas. And we are grappling this change with the new plant I, therefore, see the project as a real game changer for the whole industry.
The heart of our climate-neutral production facility is the electric ceramic tunnel kiln – a groundbreaking world first for industrial ceramic production. The energy is supplied exclusively with regeneratively generated electricity from the hydroelectric power plants of the Canadian energy supplier Hydro-Québec. With the new kiln, which is about 100 meters long, we save over 9,000 tons of CO2 per year compared to a conventional gas kiln – at full capacity.
3. What are the other advantages of the new production site in Canada?
The new site in Matane fits seamlessly into Duravit’s local-for-local strategy. The location directly on the St. Lawrence River facilitates logistics and the transport of goods. The most important raw materials for ceramic production – clay, kaolin, feldspar, and quartz – are available over short distances. This allows us to significantly reduce logistics expenses and additionally save energy from fossil sources.
Compared with importing our products from Europe, we therefore expect a reduction of our CO2 emissions in the North American market of 1,500 tons per year. Together with the electric kiln, we have a reduction potential of almost 11,000 tons of CO2 per year. That is groundbreaking!
4. What will Duravit produce in Canada?
North America is one of our growth markets. We see great development potential here, which we will serve in the future with the new production site. By 2028 we want to have reached the maximum capacity of the new plant: an annual production of 450,000 large ceramic parts. In doing so, we focus entirely on the needs of the North American market. With one and two-piece toilets, but also wall-hung toilets and washbasins. Compared to today’s data, that is almost a threefold increase. Accordingly, we need production on site – close to our customers.
5. How can you imagine the set-up of the production facility in Matane?
Since we are building the plant from scratch, we can rely on state-of-the-art production processes: The building area is around 40,000 m2. Everything is highly automated and follows the principles of Industry 4.0. As mentioned, the centerpiece is the electric ceramic tunnel kiln, while other highlights include automated transport systems, glazing robots, and an automated chamber dryer. In addition, the plant will rely entirely on die-casting technology. All this is state-of-the-art.
Despite all the automation, our future employees certainly play a decisive role. Around 240 new jobs for skilled workers will be created in Matane which will strengthen the region and actuates a growth impulse at the site. As a family business with a long-term focus, we are already looking forward to working with our future team in Canada.
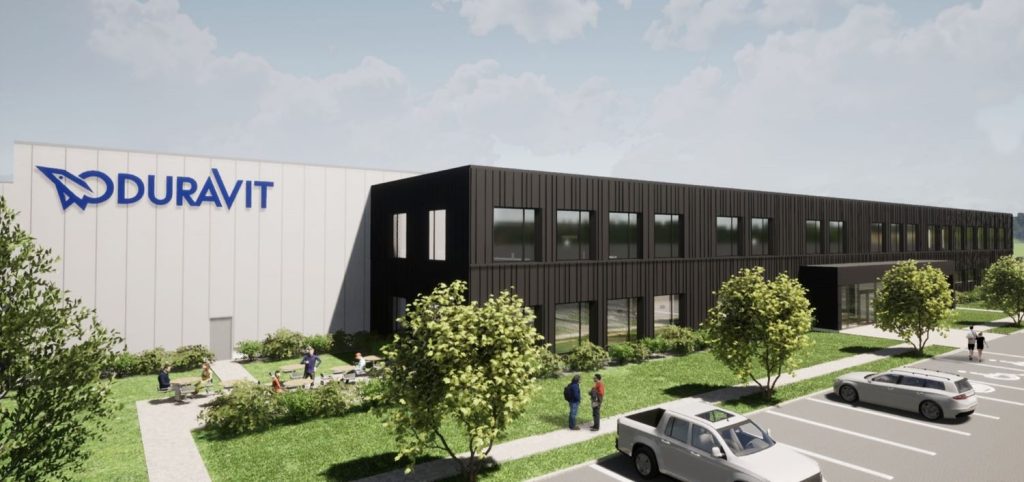